Sunday, November 18, 2007
There is Work in Progress
I'm actually spending quite a bit of time in the shop, but since most of it is gift related I am posting over at Elf Business rather than here. As I've mentioned before if you aren't on my gift list feel free to take a peek, and if you are be forewarned that you may ruin a surprise by doing that.
Sunday, November 11, 2007
New Blog
I've added a third blog to my arsenal. I'll be using it to post progress on Christmas/Hanukah projects. If you aren't on my gift list and are curious about doings in the shop take a peek. If you are on my gift list you shouldn't go there, because you'll just ruin the surprise.
You can access the new blog here.
You can access the new blog here.
Thursday, November 8, 2007
Thursday Class

Almost forgot. I also found out that the school is going to replace the equipment in the wood shop. The table saws will be replaced with SawStop table saws. The secret to the SawStop is a mechanism that detects when conductive material, like skin, comes into contact with the blade and immediately stops the blade and drops it below the table limiting the damage to the operator. There's a cool demonstration video on their web site. These are becoming a standard part of school woodshops partly because insurance companies are demanding it, and because it just makes sense. This is the saw that I'd like to add to my shop and I'm excited about the opportunity to get a chance to test drive it. My instructor wasn't clear on the time frame, so it may be awhile before I get my hands (not literally!) on the saw.
Sunday, November 4, 2007
Elf Business Update
I spent sometime today working on this year's ornament. If you're on the list to get one (you know who you are) don't peek. Anyone else can see the update here.
Thursday, November 1, 2007
LJ Sketchup Challenge
Several months ago a challenge was posted on LumberJocks. The challenge was to acquire Google's sketchup software; find a building, bridge, etc as inspiration; and design a dining room table based on that inspiration.
Sketchup is 3D modeling software. With it you can virtually construct items. Even the free version has lots of capabilities. Those capabilities make it a challenge to learn. August and September were busy and I didn't find enough energy or time to learn the software before the challenge ended at the end of September.
I also had trouble deciding on an inspiration. What I was looking for was something that had some meaning for me, and which, when worked into a table, would work. Finally with about a week until the deadline I thought of an inspiration that would work.
My inspiration is/was the Old North Bridge in Concord, Massachusetts. This is the bridge referred to as the "rude bridge that arched the flood" in the Concord Hymn by Ralph Waldo Emerson. The bridge is part of the Minute Man National Historical Park. This area was the site of one of the battles that started the Revolutionary War.
With inspiration in mind I began my work in Sketchup on the table design. It took me quite a while to conquer the software. I missed the challenge deadline (to paraphrase Douglas Adams I liked the whoosing sound the deadline made as it went flying by). I considered giving up on the design, but decided to follow through despite having missed the challenge deadline (and the prizes being given).
So, now that this has turned into a much longer story than necessary, here are a couple of pictures of the bridge. I took these from my kayak on October 18th.


This is not the bridge that was there is 1775. It would be very surprising if it was given that it's a wooden bridge. I happened to pass under the bridge while a tour was passing overhead and learned that this bridge is wider and has a higher arch than the original but the construction is basically the same.
Here's my design for a dining room table based on the bridge. If I were to build it I would use oak for the light wood and walnut for the dark wood. Construction would be primarily mortise and tenon.
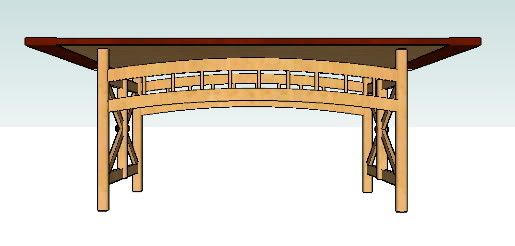

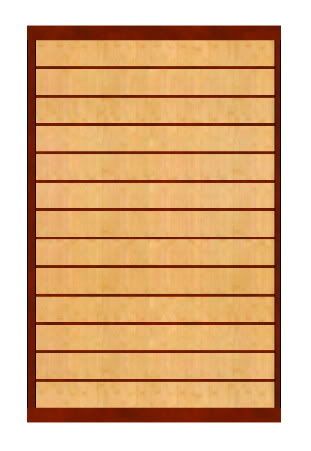

Sketchup is 3D modeling software. With it you can virtually construct items. Even the free version has lots of capabilities. Those capabilities make it a challenge to learn. August and September were busy and I didn't find enough energy or time to learn the software before the challenge ended at the end of September.
I also had trouble deciding on an inspiration. What I was looking for was something that had some meaning for me, and which, when worked into a table, would work. Finally with about a week until the deadline I thought of an inspiration that would work.
My inspiration is/was the Old North Bridge in Concord, Massachusetts. This is the bridge referred to as the "rude bridge that arched the flood" in the Concord Hymn by Ralph Waldo Emerson. The bridge is part of the Minute Man National Historical Park. This area was the site of one of the battles that started the Revolutionary War.
With inspiration in mind I began my work in Sketchup on the table design. It took me quite a while to conquer the software. I missed the challenge deadline (to paraphrase Douglas Adams I liked the whoosing sound the deadline made as it went flying by). I considered giving up on the design, but decided to follow through despite having missed the challenge deadline (and the prizes being given).
So, now that this has turned into a much longer story than necessary, here are a couple of pictures of the bridge. I took these from my kayak on October 18th.


Here's my design for a dining room table based on the bridge. If I were to build it I would use oak for the light wood and walnut for the dark wood. Construction would be primarily mortise and tenon.
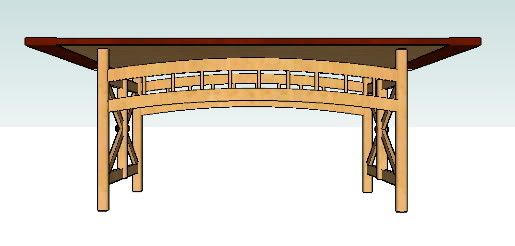
Side view.

End view.
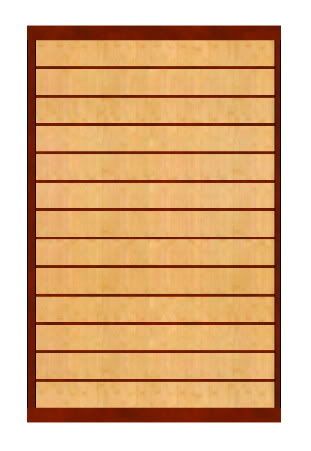
Top View. This is intended to look like the slats of the bridge surface.

A look at the whole table.
Size is 42 inches wide by 68 inches long. The legs are 28 inches high.
Size is 42 inches wide by 68 inches long. The legs are 28 inches high.
I have since used Sketchup to work out the design for the advent calendar I'm working on, and for a small side table. More details on those to come later.
Saturday, October 13, 2007
Elf Business
As my family and friends know I have been making an almost yearly ornament/window hanging since 1996 (I've missed two or maybe it's three years.). Since a number of those people read this blog I'm not going to put much about this year's creation here. Suffice it to say that the planning has begun and I don't want to spoil the surprise.
If you are not on my gift list and would like a window into the process of creating these you can follow the progress here. Those of you who are on the list, and you know who you are, do NOT follow the link. Ruining the surprise will not make you happy, it will only ruin the surprise.
If you are not on my gift list and would like a window into the process of creating these you can follow the progress here. Those of you who are on the list, and you know who you are, do NOT follow the link. Ruining the surprise will not make you happy, it will only ruin the surprise.
Thursday, October 11, 2007
Softball Bats Done

After removing the bats from the lathe the extra material was removed from each end with the band saw. A little sanding and some more oil finished them off.
Saturday, October 6, 2007
Softball Bats, Almost Done
Last spring the guys in my woodworking class got into making baseball bats. I'm not sure how it started, but 5 people including the instructor cranked out at least 1 bat. Towards the end of this the instructor mentioned that I was the one who should be making a bat since I actually play softball. At the time I was busy with other things.
Usually I take the summer off from class since I spend so much time with softball (playing, umpiring, scheduling umpires). This summer I decided it was worth the fairly low cost to have the shop available for as many nights as I could get there, so I signed up for the class. I spent most of the time working on Hiker Boy's advent calendar. I finished up the tasks I wanted to do on the advent calendar and still had a class and a half left. I didn't want to start another project, I've got more than enough waiting for completion, so I decided to give turning a bat a try.
First step was to mill blanks. This started with big slabs of ash about 4" x 10" x 3'. With help, that sucker was heavy, I cut 2 blanks about 4" square by 3' long. To make things easier on the lathe we set the blade on the table saw to 45 degrees and cut off the corners on the long edges.
This left something that looked like this:
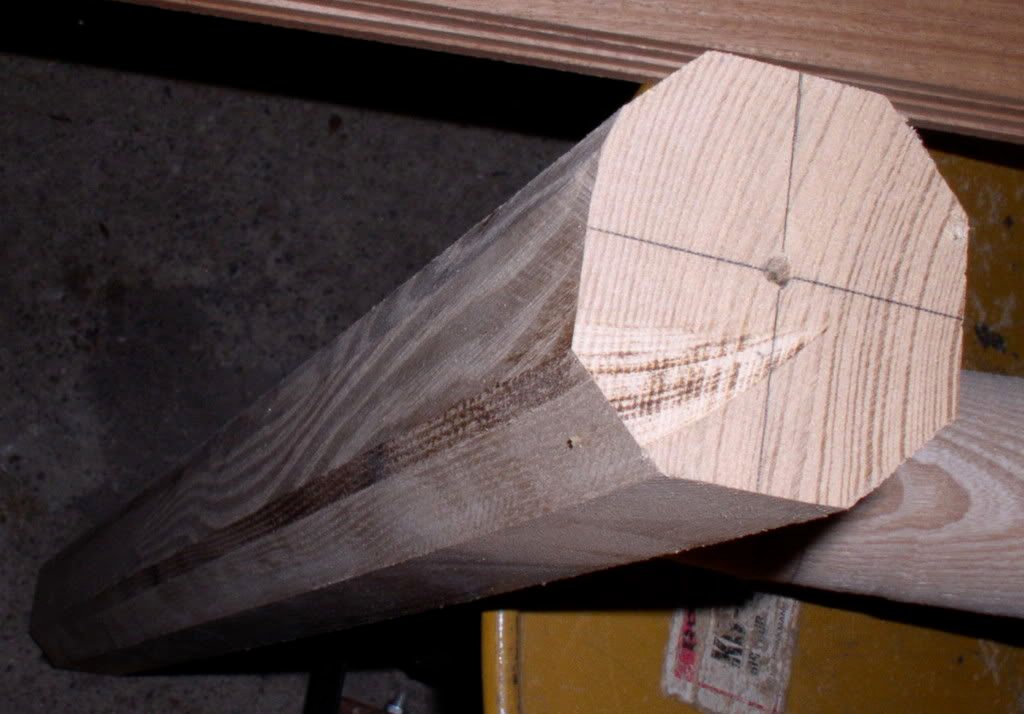
Before heading to the lathe we used a saw to cut shallow grooves on one end of the blank, where you see the lines in the picture.
First step on the lathe was to create a cylinder. This is fairly simple but messy work. I ended up with wood chips, and saw dust everywhere including down my shirt. Once I had the wood worked into a cylinder it was time to start the real work. First step was to mark the locations of diameter changes. Using my favorite aluminum bat I measured out where the barrel ended and the taper began, the length of the handle and the width of the knob. I had to shorten the wooden bat slightly because the piece of wood was slightly shorter. It's only about an inch difference, not a major issue.
Using a parting tool I made incisions to mark the transition points. Then using a variety of tools I set to work on trimming the barrel to the desired thickness, and creating the taper. I ran out of time partway through. The picture on the left is the first bat with the barrel created and the taper roughed out and a lot of wood left to remove on the handle (left) end.
It was about two months before I got back to the bat. During week one of fall classes I finished off the first bat. After finishing off the construction - thinning out the handle, creating the knob and rounding over the edges of the knob and the end of the barrel - it was time for smoothing. A short round with a couple of files, and three grits of sand paper and the bat was almost done. (I thought I was a mess with all the wood chips I acquired it the turning - sanding just took that to a whole new level.) The knob is a little small, and there are a couple of nicks in the wood but it turned out (no pun intended) pretty good for my first try.
I had made 2 blanks, so I set off on bat number 2 as soon as bat 1 got to this point. By the time I left class on that first night of the fall session I had not only the mostly complete bat 1, but the cylinder for bat 2.
Thursday night I got back to work on bat 2. The steps were the same. The difference was a little more confidence and a little more patience. Bat number 2 is a little better than bat 1. The knob is the correct size, the handle is a little thicker (on purpose) and there are no nicks.
Next week I'll work on burnishing and finishing the bats, and separating them from the excess bits that allow them to be inserted into the lathe.
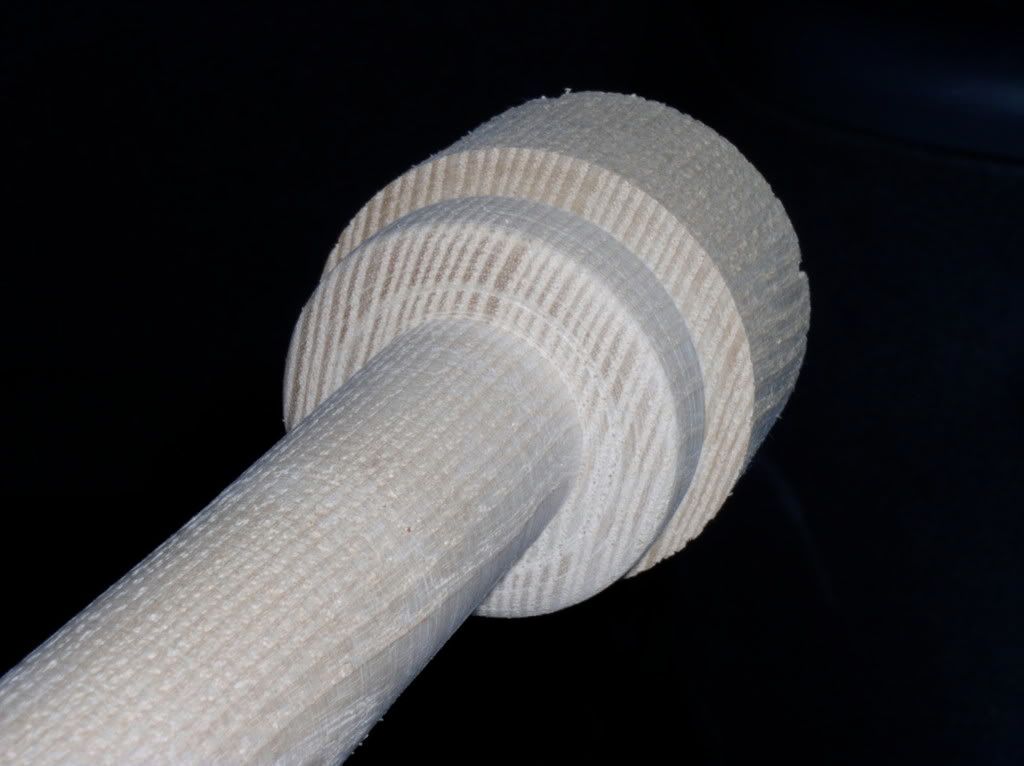
This is the knob on bat 2.
The two bats resting in my wheelbarrow. The lower bat is the first bat. If you click on the picture you can see one of the nicks near the taper.
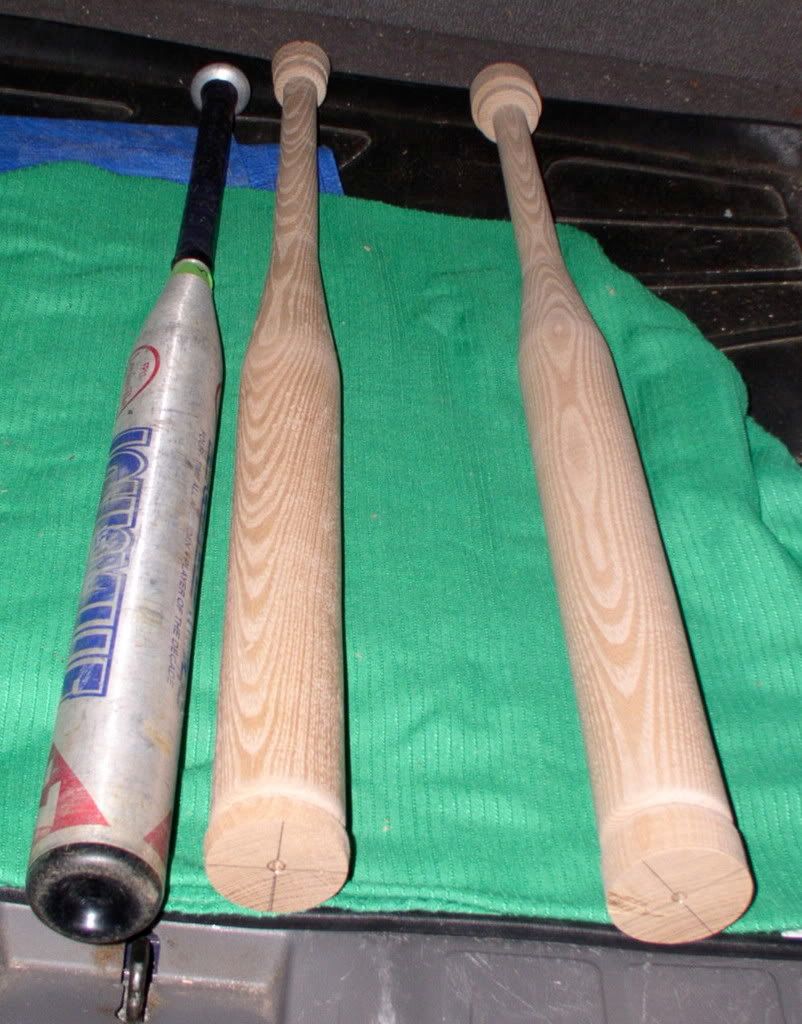
Here are both bats sitting next to the aluminum bat they are patterned after. Bat 1 is in the middle.
Glossary (definitions from dictionary.com)
lathe - a machine for use in working wood, metal, etc., that holds the material and rotates it about a horizontal axis against a tool that shapes it.
Gouge - a chisel having a partly cylindrical blade with the bevel on either the concave or the convex side. Note: the link is to a stone for sharpening a gouge but it includes a good picture of a gouge.
parting tool - a thin tool, used in turning or planing, for cutting a piece in two.
Here is a picture of a small collection of turning tools.
Usually I take the summer off from class since I spend so much time with softball (playing, umpiring, scheduling umpires). This summer I decided it was worth the fairly low cost to have the shop available for as many nights as I could get there, so I signed up for the class. I spent most of the time working on Hiker Boy's advent calendar. I finished up the tasks I wanted to do on the advent calendar and still had a class and a half left. I didn't want to start another project, I've got more than enough waiting for completion, so I decided to give turning a bat a try.
First step was to mill blanks. This started with big slabs of ash about 4" x 10" x 3'. With help, that sucker was heavy, I cut 2 blanks about 4" square by 3' long. To make things easier on the lathe we set the blade on the table saw to 45 degrees and cut off the corners on the long edges.
This left something that looked like this:
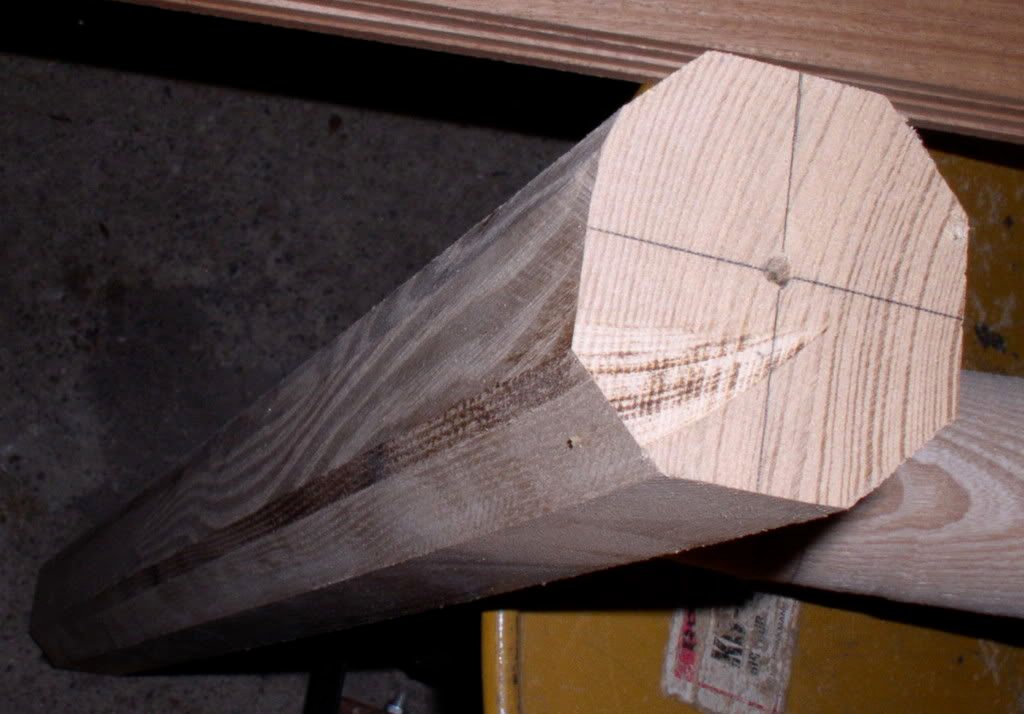
Before heading to the lathe we used a saw to cut shallow grooves on one end of the blank, where you see the lines in the picture.
First step on the lathe was to create a cylinder. This is fairly simple but messy work. I ended up with wood chips, and saw dust everywhere including down my shirt. Once I had the wood worked into a cylinder it was time to start the real work. First step was to mark the locations of diameter changes. Using my favorite aluminum bat I measured out where the barrel ended and the taper began, the length of the handle and the width of the knob. I had to shorten the wooden bat slightly because the piece of wood was slightly shorter. It's only about an inch difference, not a major issue.

It was about two months before I got back to the bat. During week one of fall classes I finished off the first bat. After finishing off the construction - thinning out the handle, creating the knob and rounding over the edges of the knob and the end of the barrel - it was time for smoothing. A short round with a couple of files, and three grits of sand paper and the bat was almost done. (I thought I was a mess with all the wood chips I acquired it the turning - sanding just took that to a whole new level.) The knob is a little small, and there are a couple of nicks in the wood but it turned out (no pun intended) pretty good for my first try.
I had made 2 blanks, so I set off on bat number 2 as soon as bat 1 got to this point. By the time I left class on that first night of the fall session I had not only the mostly complete bat 1, but the cylinder for bat 2.
Thursday night I got back to work on bat 2. The steps were the same. The difference was a little more confidence and a little more patience. Bat number 2 is a little better than bat 1. The knob is the correct size, the handle is a little thicker (on purpose) and there are no nicks.
Next week I'll work on burnishing and finishing the bats, and separating them from the excess bits that allow them to be inserted into the lathe.
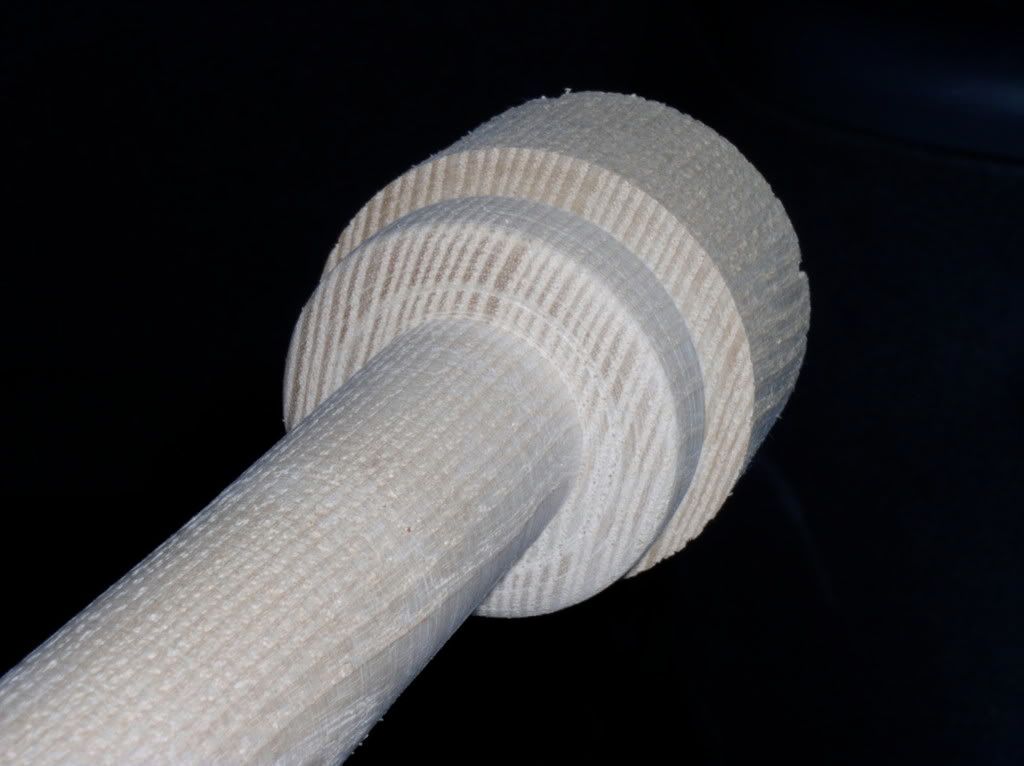
This is the knob on bat 2.

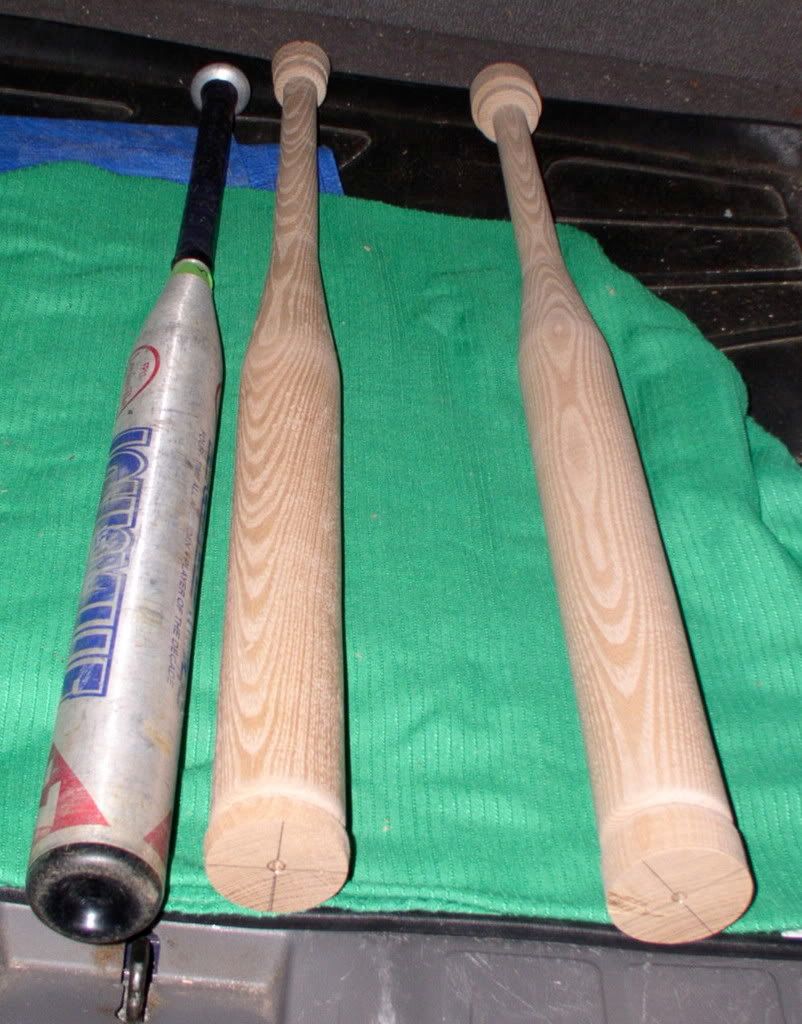
Here are both bats sitting next to the aluminum bat they are patterned after. Bat 1 is in the middle.
Glossary (definitions from dictionary.com)
lathe - a machine for use in working wood, metal, etc., that holds the material and rotates it about a horizontal axis against a tool that shapes it.
Gouge - a chisel having a partly cylindrical blade with the bevel on either the concave or the convex side. Note: the link is to a stone for sharpening a gouge but it includes a good picture of a gouge.
parting tool - a thin tool, used in turning or planing, for cutting a piece in two.
Here is a picture of a small collection of turning tools.
Saturday, September 22, 2007
Summer Woodworking
My last post was over 2 months ago. Sorry about that. I have done a bit of woodworking since then, although not a lot. Among the other things taking up my time were:
Hiker Boy's Advent Calendar
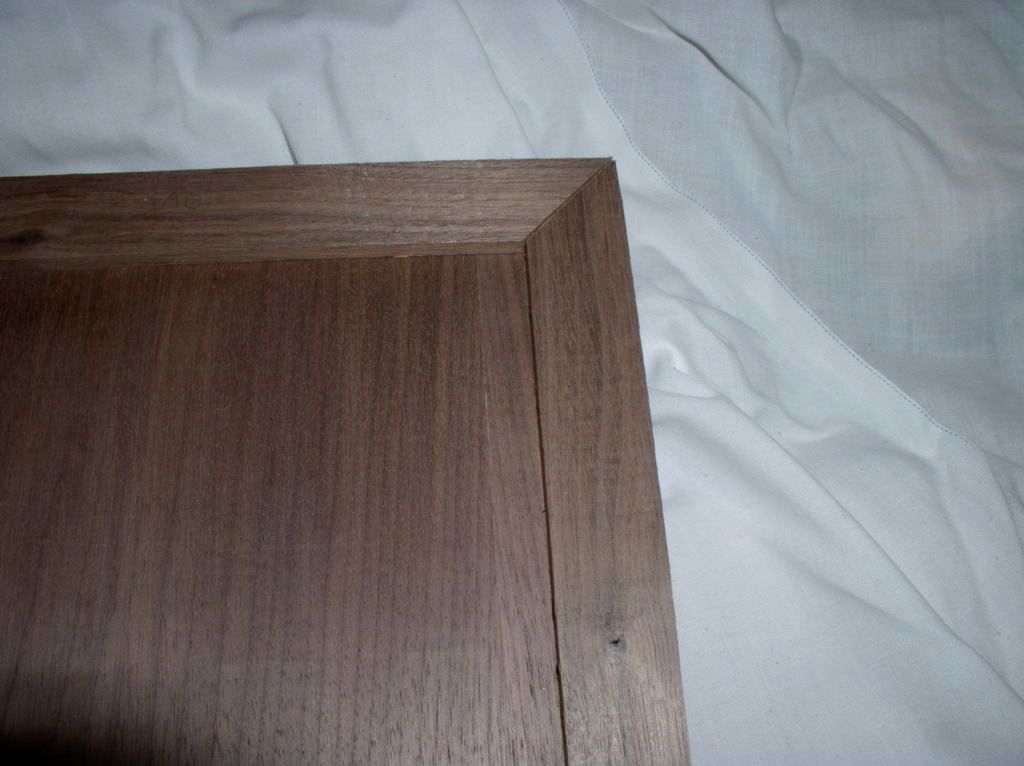
The stock for all parts has been milled, and I'm ready to start joinery. The drawer stock still needs to be cut to final dimension. The picture above is the corner of one of the doors.
Softball Bat
This is a new addition to the list. Last spring many of the guys in my woodworking class made baseball bats. One evening as I was leaving the instructor commented that I was the one who should be making a bat. He's aware of my participation in the softball league at work (I help run our team, play, umpire and coordinate the umpires for the league). And when he found out that I'd never used a lathe he was even more convinced that I should give it a try. I didn't have anything else to work on for the last class, so I decided to give it a try. Here's the progress so far. I should have it mostly finished next week when class starts again.
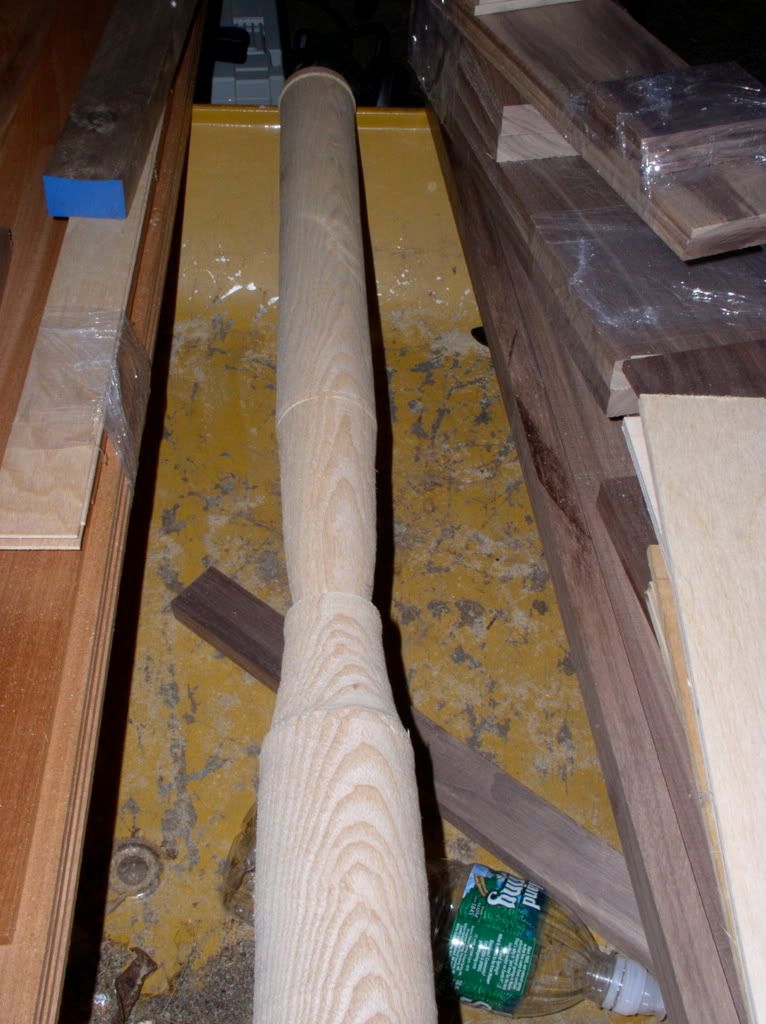
Workbench Top
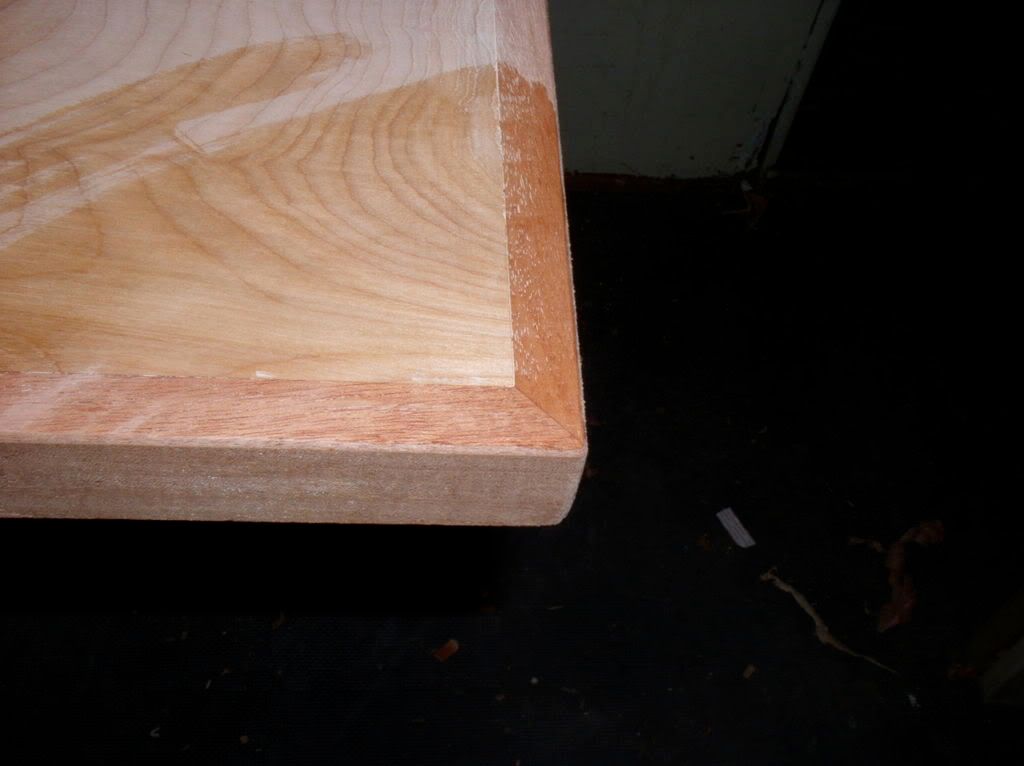
The new top for the bench is almost complete. I used mahogany to edge the plywood. It's attached using biscuits which gave me an excuse to use my biscuit joiner. I attached it so it was a little higher than the surface of the plywood and then planed it down. The only thing left to do is to apply a finish to it. I'm leaning toward using boiled linseed oil.
Footstools
I filled the grain on the footstools with a mixture of pumice and boiled linseed oil. They look great, but need a lot of sanding. I've got the top of one done and it feels great after the sanding.
Ornament
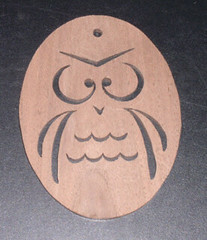
Almost every year for the last 10 I've made a window hanging/Christmas tree ornament using my scrollsaw. The one pictured above is from 2005. Much to Amy's amazement I have already got the first pass of this year's design done. I'll try this one out and then make adjustments before starting in on the production run.
- We dropped off Snowflake's nightlight and met the man himself - he's a real cutie.
- I spent a couple of days on the Cape with my sister, her family, their friend and her son. One afternoon I supervised the boys D and JT making stepping stones (concrete, ceramic tiles and glitter). JT was particularly excited about the glitter. I didn't stay long enough to see the hardened stones, but word has it that the boys were fascinated by how the gloppy concrete turned into solid stones.
- We spent the last two weeks of July in the Adirondacks. We've vacationed there all but 2 of the last 12 years, the last 8 in Owl Cabin at Wakanda. Although I took some things to sand with me they never got pulled out. I did take photos and dimensions of an end table (a new addition to our cabin) which will likely end up as a project soon.
- Like too many other houses, our bathroom has a window above the tub. Since the tub is also used for showers the window gets wet. Over the years water has undermined the window framing, and the wall behind the plastic tub surround. The surround on our tub is several panels rather than a single piece. Over time the seams have lost their integrity and water has infiltrated. As embarrassing as it is to say this, the wall board behind the surround has been falling apart for years. After replacing the toilet and floor, we finally couldn't take it anymore. So in mid-August I carefully removed the surround and replaced the outside wall. Note to anyone reading - cardboard is not an acceptable shim in a bathroom wall! The job proved a little bit more involved than anticipated because the window trim was glued to the framing which meant that it all had to be replaced.
- Since returning from vacation work has been taking up a lot of time and more energy.
- I have been giving the kayak a good amount of time in the water.
Hiker Boy's Advent Calendar
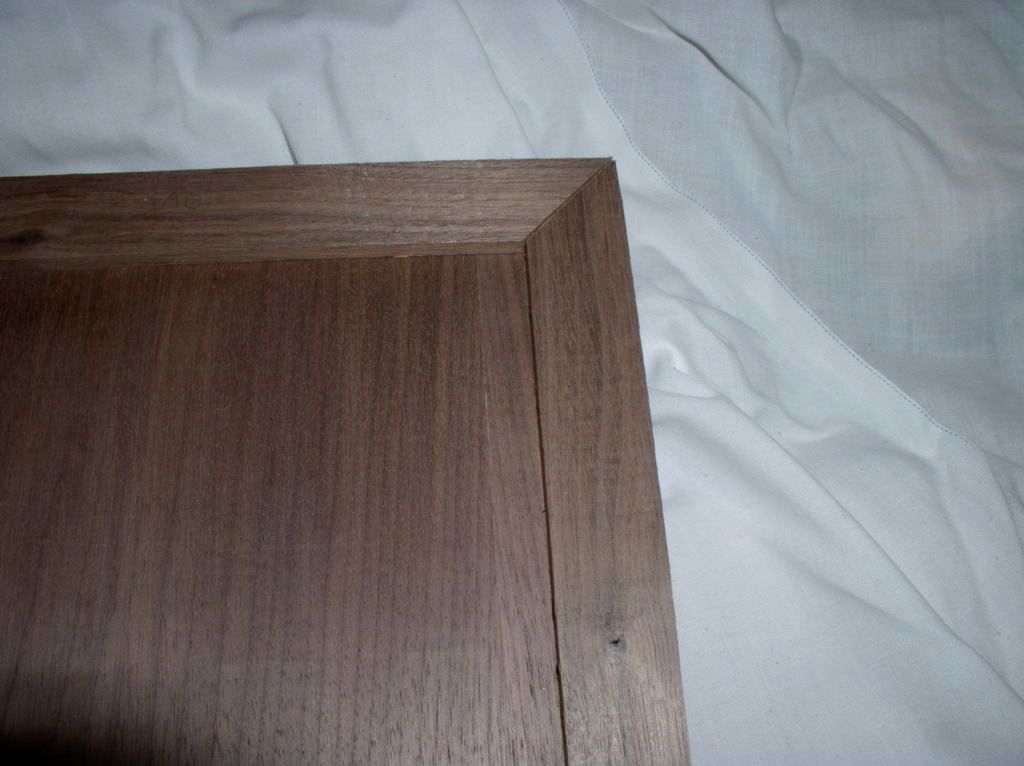
The stock for all parts has been milled, and I'm ready to start joinery. The drawer stock still needs to be cut to final dimension. The picture above is the corner of one of the doors.
Softball Bat
This is a new addition to the list. Last spring many of the guys in my woodworking class made baseball bats. One evening as I was leaving the instructor commented that I was the one who should be making a bat. He's aware of my participation in the softball league at work (I help run our team, play, umpire and coordinate the umpires for the league). And when he found out that I'd never used a lathe he was even more convinced that I should give it a try. I didn't have anything else to work on for the last class, so I decided to give it a try. Here's the progress so far. I should have it mostly finished next week when class starts again.
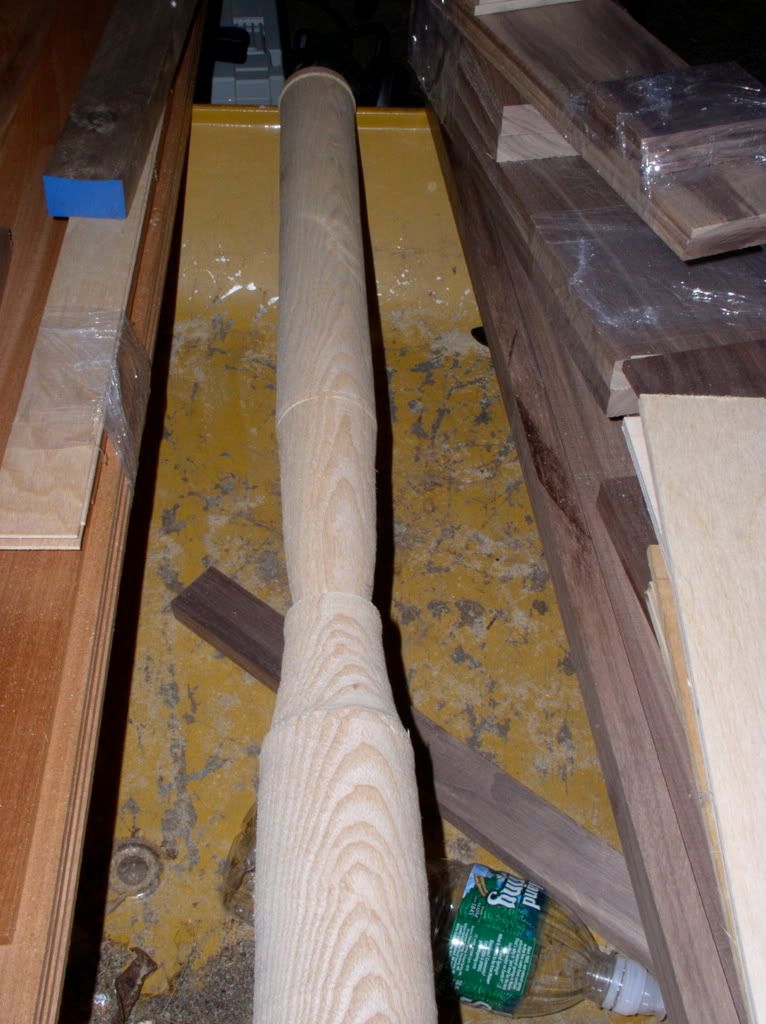
Workbench Top
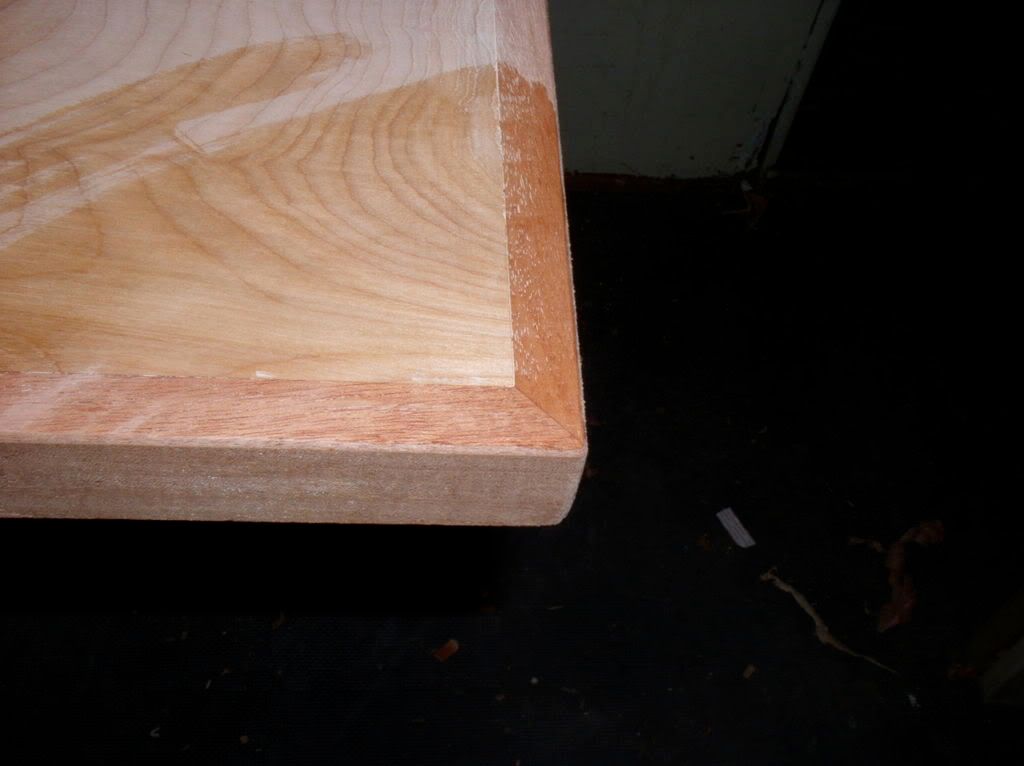
The new top for the bench is almost complete. I used mahogany to edge the plywood. It's attached using biscuits which gave me an excuse to use my biscuit joiner. I attached it so it was a little higher than the surface of the plywood and then planed it down. The only thing left to do is to apply a finish to it. I'm leaning toward using boiled linseed oil.
Footstools
I filled the grain on the footstools with a mixture of pumice and boiled linseed oil. They look great, but need a lot of sanding. I've got the top of one done and it feels great after the sanding.
Ornament
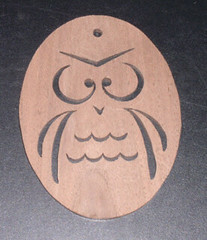
Almost every year for the last 10 I've made a window hanging/Christmas tree ornament using my scrollsaw. The one pictured above is from 2005. Much to Amy's amazement I have already got the first pass of this year's design done. I'll try this one out and then make adjustments before starting in on the production run.
Labels:
advent calendar,
foot stool,
night light,
progress,
workshop
Saturday, July 7, 2007
New Bench Top
I've been frustrated with the top of my primary workbench for quite a while. (I have a second bench but it serves as a storage area and will soon be leaving my shop.) The frame is functional, but the top which consists of 6 2X6s is not meeting my needs. I'd long ago decided that replacing the top with a double layer of 3/4" plywood would greatly improve it. I acquired the plywood back in April and it's been sitting in the garage since. A couple of weekends ago Amy helped me cut it down to the necessary size.
Last night I decided that this was the weekend to tackle the benchtop replacement. This is what it looked like when I headed to the shop today. The clutter on the top is normal, although the exact composition changes.
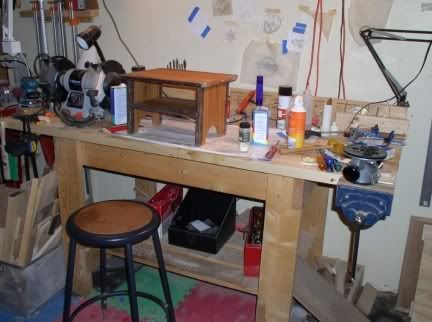
Step one of the process was to clear the bench. A number of things were put away, the rest were stacked in other places - on top of the other bench, on top of the router table, on the floor... The attached items - drill bit holder, vise, the screw from which my brush hangs and the doorbell light* were also removed. Here's how it looked at that point.
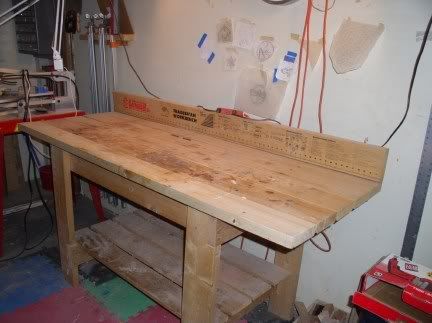
After removing the back splash, the boards of the top were removed, a fairly straight forward operation. Here's a look at the frame. The bright colored squares are rubber floor mats. I've had the floor padded for a while. I started with a small number of colored mats. When I expanded the padding all I could find were slightly larger black mats. I used both the colored mats and the new ones, but they don't interlock and this left edges to trip on which is definitely not a good idea. So, I took this opportunity to replace the colored mats with more of the black ones. This will give me fully interlocked padding.
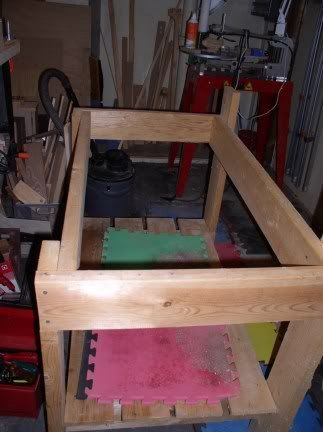
Next step was layer number 1 of the plywood. I screwed this layer to the frame, and drilled pilot holes to attach the two layers together from below which will leave no screw holes on the work surface. After screwing down this piece, Amy helped me spread glue on it. Then we added the top layer.
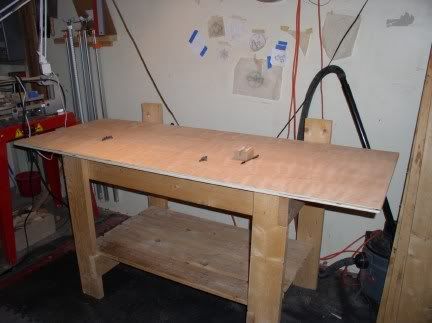
The two layers were clamped together, and screwed together from below. The pieces are attached with 5 rows of three screws. I reattached the original back splash. I'll add hardwood edging once I get some milled, probably in class on Thursday.
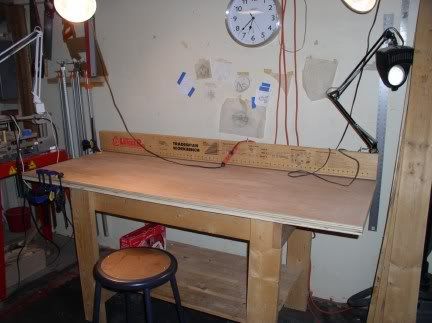
I've already put the new top to use doing the final work on Snowflake's nightlight. The light panels and the track they ride in were sanded and the track was waxed using a birthday candle - it's almost the perfect size to fit into the 1/4" wide dado. I added the light holder, and the felt which covers the bottom. A light sanding and another coat of wipe-on polyurethane finished up the work. We'll be delivering it tomorrow.
* The doorbell light is an architect style lamp which is attached to a plug which is activated by a doorbell. The doorbell is installed next to the door to the shop. Visitors to the shop can get my attention when I've got my back to the door and ear plugs in by pressing the doorbell, which makes the light blink. I acquired this from a vendor specializing in equipment for the deaf. I highly recommend it. Amy likes it because she can get my attention without coming into the shop thus avoiding the dust and some of the noise.
Last night I decided that this was the weekend to tackle the benchtop replacement. This is what it looked like when I headed to the shop today. The clutter on the top is normal, although the exact composition changes.
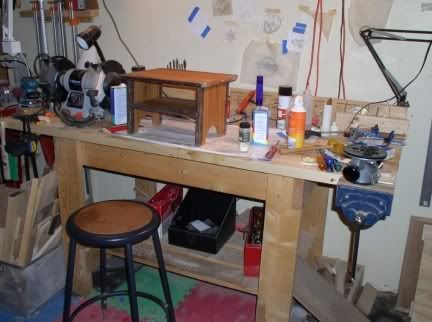
Step one of the process was to clear the bench. A number of things were put away, the rest were stacked in other places - on top of the other bench, on top of the router table, on the floor... The attached items - drill bit holder, vise, the screw from which my brush hangs and the doorbell light* were also removed. Here's how it looked at that point.
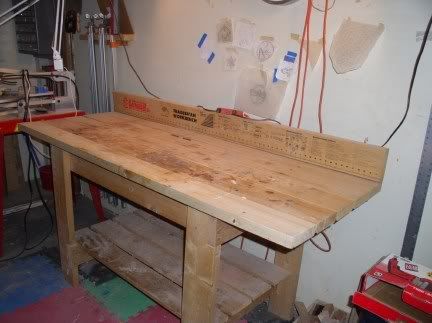
After removing the back splash, the boards of the top were removed, a fairly straight forward operation. Here's a look at the frame. The bright colored squares are rubber floor mats. I've had the floor padded for a while. I started with a small number of colored mats. When I expanded the padding all I could find were slightly larger black mats. I used both the colored mats and the new ones, but they don't interlock and this left edges to trip on which is definitely not a good idea. So, I took this opportunity to replace the colored mats with more of the black ones. This will give me fully interlocked padding.
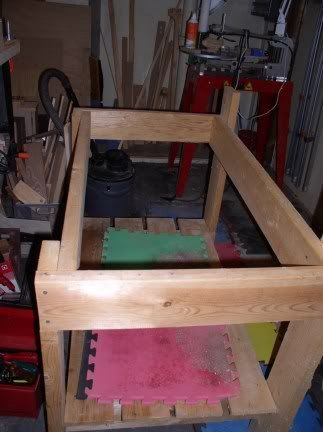
Next step was layer number 1 of the plywood. I screwed this layer to the frame, and drilled pilot holes to attach the two layers together from below which will leave no screw holes on the work surface. After screwing down this piece, Amy helped me spread glue on it. Then we added the top layer.
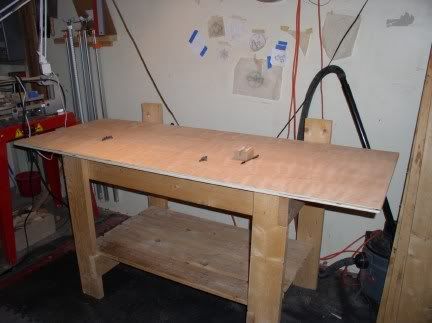
The two layers were clamped together, and screwed together from below. The pieces are attached with 5 rows of three screws. I reattached the original back splash. I'll add hardwood edging once I get some milled, probably in class on Thursday.
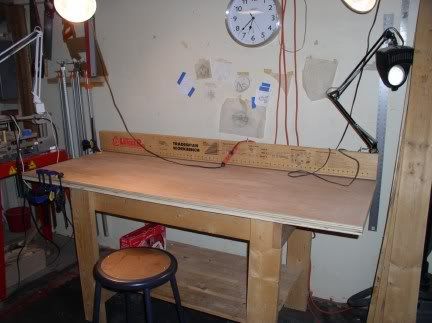
I've already put the new top to use doing the final work on Snowflake's nightlight. The light panels and the track they ride in were sanded and the track was waxed using a birthday candle - it's almost the perfect size to fit into the 1/4" wide dado. I added the light holder, and the felt which covers the bottom. A light sanding and another coat of wipe-on polyurethane finished up the work. We'll be delivering it tomorrow.
* The doorbell light is an architect style lamp which is attached to a plug which is activated by a doorbell. The doorbell is installed next to the door to the shop. Visitors to the shop can get my attention when I've got my back to the door and ear plugs in by pressing the doorbell, which makes the light blink. I acquired this from a vendor specializing in equipment for the deaf. I highly recommend it. Amy likes it because she can get my attention without coming into the shop thus avoiding the dust and some of the noise.
Friday, June 15, 2007
Current Work
I haven't been spending quite as much time in the shop since the challenge table was completed. What I have been working on is getting finish on the other projects which are ready for it.
First up is the nightlight since we don't want Snowflake to be a teenager before he gets it. I'm finishing it before I assemble it. I've got stain on all the parts. Next up is the finish coat. I'm going to go with polyurethane for that. I should get to this on Monday.
I've also done a little final sanding on the wall cabinet. I've also decided one of the doors needs a slight adjustment - it's rubbing on the bottom. That'll be a round of planing. Then I'll stain the walnut panels on the doors and the shelves which are also walnut. I think I'm going to finish it off with shellac.
Next up will be the foot stools. I've found a recipe for grain filler that uses pumice and boiled linseed oil. I've got the ingredients, just need to find a time to try it out. The grain needs to be filled because the hickory has open grain. Stay tuned for progress and pictures.
In class (Thursday nights till mid July) I've been working on hiker boy's advent calendar. Last week I remilled/recut the wood for the case. The design of this was still evolving at that point (I finished it last night) and when I first cut the case parts I forgot to leave room for drawer handles inside the case. Last night was more milling and a little bit of cutting.
When looking for a thin piece of wood there are basically 3 options - buy thin lumber which is expensive, plane a thicker piece which can waste a lot of wood, or resaw which maximizes the use of the lumber. Basically what a woodworker means when they saw they resawed a piece of lumber is that they cut the wood into thin strips.
A lot of times this is done on a band saw which has a blade that is a loop (think rubber band) with teeth on one edge. This can also be done on a table saw - usually by raising the blade to 1/2 the height of the wood and running the wood through twice. Or a combination of table saw and band saw can be used - run it through the table saw to get most of the wood cut away and finish up on the band saw.
The reason the band saw is the preferred method is the blade is much thinner so there is less waste. But because the blade is thinner it is harder to get a straight cut. It's a trade off and there are lots of products to help.
Since the piece I was resawing was not very wide (2") I just cut it in one pass on the table saw. Yes, I used a push stick! Next time I'll run the cut pieces through the planer to even them up.
On tap for next week -
First up is the nightlight since we don't want Snowflake to be a teenager before he gets it. I'm finishing it before I assemble it. I've got stain on all the parts. Next up is the finish coat. I'm going to go with polyurethane for that. I should get to this on Monday.
I've also done a little final sanding on the wall cabinet. I've also decided one of the doors needs a slight adjustment - it's rubbing on the bottom. That'll be a round of planing. Then I'll stain the walnut panels on the doors and the shelves which are also walnut. I think I'm going to finish it off with shellac.
Next up will be the foot stools. I've found a recipe for grain filler that uses pumice and boiled linseed oil. I've got the ingredients, just need to find a time to try it out. The grain needs to be filled because the hickory has open grain. Stay tuned for progress and pictures.
In class (Thursday nights till mid July) I've been working on hiker boy's advent calendar. Last week I remilled/recut the wood for the case. The design of this was still evolving at that point (I finished it last night) and when I first cut the case parts I forgot to leave room for drawer handles inside the case. Last night was more milling and a little bit of cutting.
- planed the stock for the drawer fronts
- jointed, planed and cut the stock for the door stiles and rails
- I may have to repeat this since some of the pieces sprung into a lovely curve after cutting
- jointed, planed and resawed (explanation below) stock for the drawer sides
When looking for a thin piece of wood there are basically 3 options - buy thin lumber which is expensive, plane a thicker piece which can waste a lot of wood, or resaw which maximizes the use of the lumber. Basically what a woodworker means when they saw they resawed a piece of lumber is that they cut the wood into thin strips.

The reason the band saw is the preferred method is the blade is much thinner so there is less waste. But because the blade is thinner it is harder to get a straight cut. It's a trade off and there are lots of products to help.
Since the piece I was resawing was not very wide (2") I just cut it in one pass on the table saw. Yes, I used a push stick! Next time I'll run the cut pieces through the planer to even them up.
On tap for next week -
- recutting the pieces for the door frames
- cutting plywood panels for the doors, drawer bottoms and back
- milling and cutting pieces for the drawer supports/dividers
Labels:
advent calendar,
cabinet,
foot stool,
night light,
progress
Sunday, June 3, 2007
Challenge Table: Plug Jig


The original version of the Thorsen House table, and the version published in Popular Woodworking magazine (which was the inspiration for the challenge) both include square plugs on the legs, breadboard ends, and stretchers. I had intended to include plugs on my table but time got the best of me and the plugs did not happen.
I did, however, cut the plugs. (Now I've got a pile of plugs in my shop. I'll have to find another use for them.) To ensure that the plugs were equal in size I made the jig pictured above. This jig isn't perfect, I'll get to that in a minute. First a description of this jig.
The plugs for the table are square. So I needed a way to hold the small (1/4" square) rod while accurately cutting 3/8" long plugs. I decided the safest way to cut them would be with my Nobex miter saw, which is human powered. There are two pieces which support the stock - one on each side of the saw blade, a sliding stop which runs in dadoes in side extensions, and a base.
To ensure that the holes in the support blocks were aligned I used double-sided tape to join them. Then a 1/4" hole was drilled through both. The hole was squared up with a chisel. Then the support blocks were screwed to the base, and the extension wings were screwed to one block.
To use the jig the stock is pushed through the two support blocks with the stop in the closed position (it's in the open position in the picture above). Then the plug is cut. Once the cut is complete the stop is raised and the plug is pushed out.
What I'll do differently next time:
- the jig is much taller than necessary - the next one will be shorter
- there isn't enough size in the base to easily clamp it to the saw - the base needs to be longer and deeper side extensions wouldn't hurt either
- aligning the two support blocks for screwing to the base was tricky - next time I'll make a shorter support block from a single piece of wood and cut it in two after the jig is assembled.
- chiseling the square hole accurately was difficult - next time I'll cut a 1/4" x 1/4" dado in the bottom of the support block before the support block is attached to the base, and before it's cut in two. This will also provide better support for the plug stock and limit vibration.
Challenge Table: Pictures

The top, shelf, inlay and drawer handle are walnut. The breadboards, aprons, stretchers and legs are cherry. The walnut was stained using a gel stain to even out the color. Then the entire table was covered with two coats of amber shellac.
The drawer is aspen, and the drawer runners are maple.
The aprons and stretchers join the legs with mortise and tenon joints. The top and breadboard ends are also joined with motise and tenons. The stretchers have dadoes into which fits tenons on the shelf.
The table is 22" tall and the top is 17" square.

To see the other challenge entries click here.
Thursday, May 31, 2007
Challenge Table: Complete
I'll be posting more about the construction of the table when I get some time, and more than 2 brain cells to rub together (I had vicious insomnia last night and didn't get much sleep). In the meantime head on over to my LumberJocks project post to see pictures of the completed table and a description of it.
Night light
Tuesday, May 29, 2007
Lots of Progress
I have been remiss in not posting about all of the progress I've made in the last month of so. Here's a recap by project.
Wall Cabinet
The wall cabinet is ready for finish.
Foot Stools
The foot stools are ready for finish. I've been wondering about how to fill the grain, since the hickory has a very open grain pattern. While looking for something else in my stash of saved woodworking magazine articles I found one I'd saved on non-commercial grain filler. One option is to use pumice and boiled linseed oil. I've had a box of pumice sitting on the shelf for years (for use as a sanding agent when finishing) so I bought a can of boiled linseed oil. I'm going to give this a try before adding finish to the stools.
Night Light
Ready for finish. The panels look great (pictures soon). I'm going to apply finish before I glue up the box, so I have more control over the finish. I need to get this done ASAP since Snowflake made his appearance 3 weeks ago.
Hiker Boy's Advent Calendar
I've got the plan sketched out and started cutting the parts during my last couple of classes. I've got the sides of the case ready, although I may have to check that I left room to affix the back.
CD Holder
Adjusted the height of the dividers. It's ready for dadoes and rabbets.
Challenge Table
This has been garnering most of my attention. I started to include a report here, and then realized that it make this post extremely long. So, I'll post about that separately.
Wall Cabinet
The wall cabinet is ready for finish.
Foot Stools
The foot stools are ready for finish. I've been wondering about how to fill the grain, since the hickory has a very open grain pattern. While looking for something else in my stash of saved woodworking magazine articles I found one I'd saved on non-commercial grain filler. One option is to use pumice and boiled linseed oil. I've had a box of pumice sitting on the shelf for years (for use as a sanding agent when finishing) so I bought a can of boiled linseed oil. I'm going to give this a try before adding finish to the stools.
Night Light
Ready for finish. The panels look great (pictures soon). I'm going to apply finish before I glue up the box, so I have more control over the finish. I need to get this done ASAP since Snowflake made his appearance 3 weeks ago.
Hiker Boy's Advent Calendar
I've got the plan sketched out and started cutting the parts during my last couple of classes. I've got the sides of the case ready, although I may have to check that I left room to affix the back.
CD Holder
Adjusted the height of the dividers. It's ready for dadoes and rabbets.
Challenge Table
This has been garnering most of my attention. I started to include a report here, and then realized that it make this post extremely long. So, I'll post about that separately.
Labels:
cabinet,
cd holder,
foot stool,
night light,
progress
Thursday, May 24, 2007
Planer & Jointer Uses

Unless you buy wood already surfaced - which at a lumberyard is expensive and at the big box stores is low quality - the wood will look like the picture at the left. This may not look so nice but once it's cleaned up it should look pretty good, although I surfaced a board last week that had the wildest grain and color patterns. Might be good for some things, but not for the cabinet door frame I'd intended it for. But I digress.. The way you take this rough board and make it a nice pretty board is either to use a hand plane or the power tool option the planer and jointer (you may also see this written as joiner).

Step 1 is to take the board to the jointer and place the face side down. For safety you determine which face is most stable and place that down on the infeed table of the jointer. With one edge against the fence you push the board across the blades (the three lines in the circle on the drawing below) to the outfeed table. The outfeed table is just a bit higher than the infeed table and the blades are aligned with the outfeed table.

The amount of difference between the tables is the amount of wood that is removed. After several passes over the blades the face of the board should look something like the wood pictured below, but with rough edges.

Then it's time to head to the planer. The planer also has a cylinder with blades on it, but instead of two tables it has one.

Friday, May 11, 2007
Class Machines
I prepare the stock for my projects in the adult ed class I take at a local high school. The equipment is decent, although the upkeep could be better. Last fall both the jointer and planer were out of commission for several weeks. Given that the use of those machines and the tablesaw are the reason I take this class, it was frustrating to say the least.
I first took this class about 10 years ago, after winning a gift certificate in a raffle which was part of the annual charity fund raising at work. I've taken it at least one session almost every year since.
I first took this class about 10 years ago, after winning a gift certificate in a raffle which was part of the annual charity fund raising at work. I've taken it at least one session almost every year since.
Pictured below are the machines I use most often at class, and a brief explanation of each.
This is the jointer. It's used to create a flat face, or edge on a board. Step one in surfacing a board is to place it on it's face on the table to the right of the red guard. The table surface on the right is slightly lower than the table surface on the left. The blades are under the red guard attached to a cylindrical holder. The blades spin and as you push the board from right to left they shave a small amount off the wood. Once one face is flat, the board is held on edge against the fence (the vertical metal piece in the picture), and run over the blade. As long as the fence has been set at a 90 degree angle to the table this will create an edge square to the face.


Sunday, May 6, 2007
The Spark
In a comment on one of my posts, self taught artist asked about how I got started in woodworking. I've written some of this before on LumberJocks, but will repeat and expand on it here. I'm going to start with some background, bear with me it is relevant.
When I was 4 my family moved into a haunted house. The house had had only 2 previous owners, the architect who built it for himself only to run out of money, and the woman my parents bought it from. Mrs. M.'s parents bought it for her as her dowry. When my parents bought it Mrs. M. was 90 something and headed for a nursing home. The house had not had much done to it in years. It was at the end of a dead-end street, a dark brown Dutch colonial. The only occupant an old woman, and my guess is that fear made her come across as mean.
My parents bought that house because of location - there was a good elementary school within walking distance and my father could walk to work, size - this house was big with a full attic and basement, and I'm sure cost - because of the work it needed it was less expensive than other houses in the area.
Once we moved in my parents got to work fixing the house up. Wall paper was removed, paint added to walls and the like. And this is where my grandfather enters the picture. Granddaddy Art worked in the building trades. He didn't live close by, but as long as there was apple pie for dessert he would put his expertise to work for my parents. He was also adept at salvage so when my parents decided to replace the claw foot tub in the bathroom with a more modern model he acquired one. I have vivid memories of riding home down the Massachusetts Turnpike in the back of the new bathtub.
Granddaddy Art would come for several days or a week to help with the rehabilitation of that house - fixing the wainscoting on the front stairs, rebuilding the chimney, ... I loved to watch this work. Although he worked on our house I don't have an image of my father building things . Granddaddy Art built things. We spent part of most summers at his "camp" in the Berkshire hills - a cabin he'd built. Later I learned that he'd salvaged a house from one of the towns on the site of the Quabbin Reservoir and reassembled it for his family on a lot in Springfield. His grave is in site of that house.
When Granddaddy Art was at our house I would follow him around, not too closely as that would get me in trouble. I can remember sitting on the basement stairs while he and my father worked on some creation, and standing on a ladder with my head peeking out of the hatch in the attic watching him rebuild the chimney. I was always curious about what he was doing, but never learned any secrets from him. He was a traditional sort and construction wasn't a vocation he thought suitable for girls.
I think it was watching him that gave me the confidence to think that I could make things. I'd seen it done and it didn't look so hard. That was the spark, and it's why this blog has the name it does.
One regret I have is that he died and his tools were sold off, before I caught the woodworking bug. I would love to have tools from his shop, or to have learned from him. I'd like to think that he'd have mellowed by now and would be proud of the things I build.
When I was 4 my family moved into a haunted house. The house had had only 2 previous owners, the architect who built it for himself only to run out of money, and the woman my parents bought it from. Mrs. M.'s parents bought it for her as her dowry. When my parents bought it Mrs. M. was 90 something and headed for a nursing home. The house had not had much done to it in years. It was at the end of a dead-end street, a dark brown Dutch colonial. The only occupant an old woman, and my guess is that fear made her come across as mean.
My parents bought that house because of location - there was a good elementary school within walking distance and my father could walk to work, size - this house was big with a full attic and basement, and I'm sure cost - because of the work it needed it was less expensive than other houses in the area.
Once we moved in my parents got to work fixing the house up. Wall paper was removed, paint added to walls and the like. And this is where my grandfather enters the picture. Granddaddy Art worked in the building trades. He didn't live close by, but as long as there was apple pie for dessert he would put his expertise to work for my parents. He was also adept at salvage so when my parents decided to replace the claw foot tub in the bathroom with a more modern model he acquired one. I have vivid memories of riding home down the Massachusetts Turnpike in the back of the new bathtub.
Granddaddy Art would come for several days or a week to help with the rehabilitation of that house - fixing the wainscoting on the front stairs, rebuilding the chimney, ... I loved to watch this work. Although he worked on our house I don't have an image of my father building things . Granddaddy Art built things. We spent part of most summers at his "camp" in the Berkshire hills - a cabin he'd built. Later I learned that he'd salvaged a house from one of the towns on the site of the Quabbin Reservoir and reassembled it for his family on a lot in Springfield. His grave is in site of that house.
When Granddaddy Art was at our house I would follow him around, not too closely as that would get me in trouble. I can remember sitting on the basement stairs while he and my father worked on some creation, and standing on a ladder with my head peeking out of the hatch in the attic watching him rebuild the chimney. I was always curious about what he was doing, but never learned any secrets from him. He was a traditional sort and construction wasn't a vocation he thought suitable for girls.
I think it was watching him that gave me the confidence to think that I could make things. I'd seen it done and it didn't look so hard. That was the spark, and it's why this blog has the name it does.
One regret I have is that he died and his tools were sold off, before I caught the woodworking bug. I would love to have tools from his shop, or to have learned from him. I'd like to think that he'd have mellowed by now and would be proud of the things I build.
Thursday, May 3, 2007
Thursday - Class Night
I ran through all the work I had planned for class pretty quickly tonight.
Here's what I did:
Here's what I did:
- Cut extra panels sized to the nightlight light panels. I'll use these to back up the panels when I scrollsaw them this weekend.
- Cut the shoulders for the tenons on the table parts - aprons, top, stretchers.
- Planed the filler for the mortises, which I'll use to fill the first tenon while cutting the second in the legs.
- Cut parts for a new project - a small box for the bathroom to replace the basket that's we used have on the back of our toilet before we replaced the toilet.
- Trimmed the shelves for the wall cabinet.
Tuesday, May 1, 2007
Mortises, Mortises, Mortises

I'm working on cutting the mortises for the challenge table. There are three in each of the breadboard ends, two each in the front legs, and three each in the back legs. For those keeping count that's 16 mortises.

I decided to finish the mortises on my router table. First up was the purchase of a new 3/8" straight router bit which I did a few weeks ago. I hadn't realized how dull my router bits are until I loaded this one up in my router and made a test cut. So I've added finding a service to sharpen my router bits to my to-do list.
With the new bit in the router, I set the fence. I'm using Norm's method of cutting each twice - running each face of the wood against the fence to ensure that the mortise is centered. This is possible because I haven't yet cut the tenons, so I'll be able to create those based on the thickness of the mortises. Last night I milled the remaining mortises on the breadboard ends. Tonight I finished marking the mortises on the legs, and began the cutting. I decided to start by drilling out most of the waste out with my drill. I chucked a drill bit which is slightly smaller than the final width of the mortise into my drill and started drilling.
I thought I'd carefully measured the depth I needed, but clearly I should have triple-checked it. The drill went completely through the leg! This wouldn't have been that bad except that it chipped out the face which was intended to be left solid. After creating a plug to fill the errant hole, and readjusting which leg is which and which face is the intended outer face I got back to the job at hand. First up - remarking the drill bit, then after cutting a whole lot of holes - one mortise on each leg is 4 1/2" long.
Finally, after checking the router fence using a piece of scrap leg stock, I started working the mortises on the router table. It's going quickly since I've already removed the bulk of the waste. I've got 3 more passes to make on this face of the legs.
On the back legs there are two mortises which intersect - one faces the other back leg, the other faces the front legs. This leaves a very small section of wood on the inner corner of the leg and requires very careful cutting. In preparation for this I've milled a board to fill the mortise that's already been cut and support that small section of wood (come back later for a picture). That wood is a little too thick so I'll need to do some planing/sanding before I start on the other two mortises.

Update 5/3 - Added pictures.
Monday, April 30, 2007
Wall Cabinet: Almost Done
I have made progress on the wall cabinet in the last week or so, but it has been agonizingly slow. After finishing the hinge mortises I began work on the stop and latch mechanism.
I added a thin stop, 1/16" thick, at the bottom of the cabinet. It's glued to the inside. I measured carefully, marked where it needed to go, and glued it in. And then I had to remove it and replace it. At this point I can't remember why.
The upper stop/latch mechanism is more substantial. It consists of a 3/4" X 1/2" X 3" block with two super strong magnets super-glued into it. The doors each have a magnet washer screwed into the inside corner. I wasn't paying enough attention when I drilled the recess for the magnet washers, and managed to get one on the hinge edge of the door instead of the non-hinge edge. That happened to be the first one and I'd used super-glue to attach it. That boo-boo is now covered with a circle of veneer.
Again I carefully marked and measured the location of the stop block/latch on the inside of the cabinet, and transfered the measurements to the top. I'm attaching the block with screws from the top. The holes are then filled with plugs. So in attempt number 1 I drilled the pilot holes, applied glue to the block, screwed it in, clamped it for good measure and left it to set.
The next day I took off the clamps and closed the doors to check on the alignment. Imagine my surprise when the doors wouldn't shut. I quickly surmised the the problem. When I transfered the measurements from inside the cabinet to the top, I forgot to take into account that the screw holes need to be in the center of the block. The line I'd transferred and drilled along was the marking for the front of the block - not the center.
Fixing this required - drilling out the plugs, removing the screws and sawing off the block. After constructing another block and marking the lines again, I screwed on the block - no glue this time - as a dry fit. The fit was perfect so I removed the block, added glue and screwed it back into place. And just in case I decided to wait before plugging the screw holes. I did super-glue in the magnets, though. All looked good, and I headed upstairs for the night.
Next time I made it into the shop, I discovered that gravity had been at work. The magnets in the stop/latch are recessed into flat bottomed holes. When the stop is attached to the cabinet they are on edge. When I'd left the shop after attaching the stop and gluing in the magnets I'd left the cabinet upright. One of the magnets had not set before I left and had slid out so that it rested at about a 45 degree angle to the block - and then it set. This was just not going to work because the door couldn't shut with the extra impediment of the angled magnet.
My first attempt at a fix was to cut off the portion of the block with the angled magnet and replace just the portion. This proved to be impossible to do well given the limited space inside the cabinet. So I unscrewed and sawed off block #2.
With block number 3, I first dry fit it to ensure it's correct placement. Then glued in the magnets with it independent of the cabinet. And finally glued and screwed it into place in the cabinet. Once it was I added the plugs.
As they say third times the charm.
All that is left to do if finish sizing the shelves. Although I built the cabinet according to the plans, the shelves are too wide! At the current width there is not enough clearance for the doors to shut when the shelves are in place.
Other than finish, and a little sanding, the shelf sizing is the last work to do on the cabinet.
Now I just have to figure out what to do with it. I built it for the experience, not with any plan for its use.
I added a thin stop, 1/16" thick, at the bottom of the cabinet. It's glued to the inside. I measured carefully, marked where it needed to go, and glued it in. And then I had to remove it and replace it. At this point I can't remember why.
The upper stop/latch mechanism is more substantial. It consists of a 3/4" X 1/2" X 3" block with two super strong magnets super-glued into it. The doors each have a magnet washer screwed into the inside corner. I wasn't paying enough attention when I drilled the recess for the magnet washers, and managed to get one on the hinge edge of the door instead of the non-hinge edge. That happened to be the first one and I'd used super-glue to attach it. That boo-boo is now covered with a circle of veneer.
Again I carefully marked and measured the location of the stop block/latch on the inside of the cabinet, and transfered the measurements to the top. I'm attaching the block with screws from the top. The holes are then filled with plugs. So in attempt number 1 I drilled the pilot holes, applied glue to the block, screwed it in, clamped it for good measure and left it to set.
The next day I took off the clamps and closed the doors to check on the alignment. Imagine my surprise when the doors wouldn't shut. I quickly surmised the the problem. When I transfered the measurements from inside the cabinet to the top, I forgot to take into account that the screw holes need to be in the center of the block. The line I'd transferred and drilled along was the marking for the front of the block - not the center.
Fixing this required - drilling out the plugs, removing the screws and sawing off the block. After constructing another block and marking the lines again, I screwed on the block - no glue this time - as a dry fit. The fit was perfect so I removed the block, added glue and screwed it back into place. And just in case I decided to wait before plugging the screw holes. I did super-glue in the magnets, though. All looked good, and I headed upstairs for the night.
Next time I made it into the shop, I discovered that gravity had been at work. The magnets in the stop/latch are recessed into flat bottomed holes. When the stop is attached to the cabinet they are on edge. When I'd left the shop after attaching the stop and gluing in the magnets I'd left the cabinet upright. One of the magnets had not set before I left and had slid out so that it rested at about a 45 degree angle to the block - and then it set. This was just not going to work because the door couldn't shut with the extra impediment of the angled magnet.
My first attempt at a fix was to cut off the portion of the block with the angled magnet and replace just the portion. This proved to be impossible to do well given the limited space inside the cabinet. So I unscrewed and sawed off block #2.
With block number 3, I first dry fit it to ensure it's correct placement. Then glued in the magnets with it independent of the cabinet. And finally glued and screwed it into place in the cabinet. Once it was I added the plugs.
As they say third times the charm.
All that is left to do if finish sizing the shelves. Although I built the cabinet according to the plans, the shelves are too wide! At the current width there is not enough clearance for the doors to shut when the shelves are in place.
Other than finish, and a little sanding, the shelf sizing is the last work to do on the cabinet.
Now I just have to figure out what to do with it. I built it for the experience, not with any plan for its use.
Thursday, April 19, 2007
Wall Cabinet Progress
No pictures tonight, I'll try to post some tomorrow.
I've finished the hinge mortises.
Next step was to adjust the fit of the doors, which were too wide. In the grand scheme of things this is a much better option than too narrow.
While taking a break at work this afternoon, I'd read a discussion on the LumberJocks website about jointing the edge of a board with a handheld router as an alternative to doing it with a split fence on a router table. I've never done either but the fence which came with my router table has a split fence option. So, I decided to give it a try. I started on a piece of scrap. That went well, so I took a deep breath and ran the first door through. It wasn't perfect but it's pretty good. The second door looks even better. So now I have a new technique I can use.
After reattaching the hinges (while listening to, of all things, Donny Osmond on the radio!) I began work on the mechanism to hold the doors shut. I'm going to use rare earth magnets and magnet washers (basically thick washers that are attached with screws. I marked the doors, and drilled the holes for the washers with a forstner bit, and attached the washer in the first door. Amy came down while I was working on this and while I was explaining what I was doing I discovered that I had put the washer on the wrong side of the door. This wouldn't be too much of a problem except I'd decided to use a little super glue to help hold the washer.
I finished up the washer on the second door and the second washer on the first door. Now I just have to figure out how to mask the second washer on the first door.
The construction phase of this project is almost complete. I need to finish trimming the shelves for width (they're a little wide), ease edges on the doors and the case, and attach the block with the magnets which will act as the latch. That's it - the end is in sight.
I've finished the hinge mortises.
Next step was to adjust the fit of the doors, which were too wide. In the grand scheme of things this is a much better option than too narrow.
While taking a break at work this afternoon, I'd read a discussion on the LumberJocks website about jointing the edge of a board with a handheld router as an alternative to doing it with a split fence on a router table. I've never done either but the fence which came with my router table has a split fence option. So, I decided to give it a try. I started on a piece of scrap. That went well, so I took a deep breath and ran the first door through. It wasn't perfect but it's pretty good. The second door looks even better. So now I have a new technique I can use.
After reattaching the hinges (while listening to, of all things, Donny Osmond on the radio!) I began work on the mechanism to hold the doors shut. I'm going to use rare earth magnets and magnet washers (basically thick washers that are attached with screws. I marked the doors, and drilled the holes for the washers with a forstner bit, and attached the washer in the first door. Amy came down while I was working on this and while I was explaining what I was doing I discovered that I had put the washer on the wrong side of the door. This wouldn't be too much of a problem except I'd decided to use a little super glue to help hold the washer.
I finished up the washer on the second door and the second washer on the first door. Now I just have to figure out how to mask the second washer on the first door.
The construction phase of this project is almost complete. I need to finish trimming the shelves for width (they're a little wide), ease edges on the doors and the case, and attach the block with the magnets which will act as the latch. That's it - the end is in sight.
Monday, April 16, 2007
Wall Cabinet: Hinges

Hinge mortises are one of those things which I do by hand. One of these years I may create a jig to do these with my router, but for now I'm content to do them by hand. I'd started them last weekend (I think). I finished up the mortises on the doors today. You may notice a very small sliver of wood at the back of the mortise in the picture. To prevent this from blowing out I clamped a piece of scrap to that edge to back it up while I was cutting.
I also spent a fair amount of time resharpening my chisel during the cutting of the mortises. The maple that the door frames are made of is hard and dulls the chisel pretty quickly.

Since I had to wait for the glue to set, I then spent a little time on the stops for the doors. And then there was a small shop accident. While retrieving a clamp from the router table I tripped (not sure if I tripped on the router table or my own feet). I landed on my knee and shoulder on the recently padded floor. See here for the impetus for the padding. The padding helped but I've still got a really unhappy knee. The shoulder doesn't seem too sore. As a result I spent quite a bit of time in commune with an ice pack.
I did make it back into the shop, after promising Amy that I would be extra super careful. I trimmed and sanded the plugs and finished the mortises on the case for one of the doors. I should be able to complete the mortises for the other door on my next trip to the shop. Then I'll be able to determine if any more trimming is needed on the doors. The last bits of construction will be to attach the stop/latch to the inside center of the top and attach the knobs. Then it's on to finishing.
Monday, April 9, 2007
Lumberjocks Thorsen Table Challenge
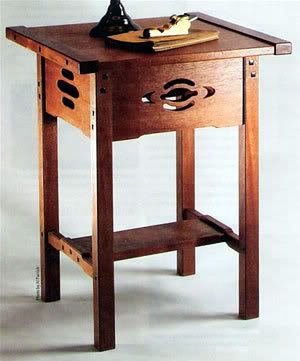
Pictured above is the table that is the basis for the Lumberjocks challenge mentioned here. I decided to jump in and take the challenge.

The second picture is the actual Greene & Greene table which was the inspiration for the table in Popular Woodworking magazine.
The table I'm making will be closer to the first than the second. I'm adding a full shelf, though and making one more change which I'm keeping up my sleeve until I'm further along.
So far I've planned my version of the table and milled the parts. I've glued up the blanks for the top and the shelf. This week in class I'll cut the aprons to length, and cut the mortises in the legs and breadboard ends. I also need to create a jig to create the detail on the edges of the aprons. Mine'll be cherry and walnut another departure from both of the pictured tables.
Saturday, April 7, 2007
Progress Passover Week

Wall Cabinet
Construction on the wall cabinet doors is done (see below), the cabinet sides have been trimmed - they were slightly too tall, and I cut pocket screw slots to attach the sides to the the top and the bottom. I also eased the edges of the top, bottom and the shelves.
Night Light
All the parts are cut, except the sides. I've got the stock for the sides cut to width, but still need to cut a series of dadoes in them. I started to do this on Wednesday, but discovered to my great chagrin that I had cut the stock 1/2" too narrow. I'd cut it down on Tuesday and still had the cut off, so I glued that piece back on. Thursday night at class I ran it through the planer to clean it up so now I can cut the dadoes. Once the dadoes, 4 in all, are cut I can cut the individual sides from the stock. After that the major work will be scrolling the light panels.
Challenge Table
After much deliberation I decided to accept the Lumberjocks Thorsen Table Challenge. I acquired the stock and firmed up my plans on Wednesday. Much of my time at class on Thursday was spent cutting parts for the table. I've got legs, breadboard ends for the top, stretchers, apron stock which still needs to be cut into individual aprons, blanks for the shelf and top which need to be glued (the shelf is drying now), and the parts for the drawer. The picture above shows the apron stock, the legs, breadboards and stretchers.
Friday, April 6, 2007
Wall Cabinet Coming Together

Woodworking lesson, or what do you mean by bookmatched?
Bookmatched panels are cut from a single board. For example: Start with a board 2" thick is sliced into two 1" thick pieces. The pieces are separated by opening the original board like a book. This creates two pieces on which the grain patterns are mirror images. If you look closely at the picture to the left you'll see this effect in the grain on the walnut panels.
Bookmatching explanation. Click for larger view.

Sunday, April 1, 2007
Sunday Progress

In the shop I worked on the sizing the strips which will hold the panels in the doors of the wall cabinet.
The doors have a rabbet that runs around the inside of the door to hold the panel. To hold the panel from the back I'm using strips that will be pinned in place with brads.
I finished cutting the miters in the strips for one door. I may have to narrow the strips, so that the door handles and hinges will fit. I'll decide on that the next time I'm down in the shop. In the oops category I discovered that I miscalculated and didn't cut enough stock for both doors. The source of the miscalculation is the miter. I forgot to calculate the lengths based on the outside of the strips, rather than the inside.

I also glued up the panel for the top of Snowflake's night light.

Subscribe to:
Posts (Atom)